In industries ranging from construction and manufacturing to healthcare and beyond, the critical role of safety gear cannot be overstated. Workers in these fields are exposed to a variety of hazards, and proper safety equipment is essential for safeguarding their health and preventing injuries. Helmets, gloves, goggles, and other protective gear are designed to mitigate the risks associated with their specific tasks, ensuring that employees can perform their duties with confidence.
However, having high-quality safety gear is only part of the equation. Regular maintenance and inspection are equally important so that this equipment remains effective over time.
R.P. Comtrade, a leader in the safety gear industry, underscores the importance of not just providing top-tier equipment but also ensuring its ongoing maintenance. They understand that maintaining the integrity of protective equipment is key to ensuring that it performs optimally when needed most.
Let’s explore in detail why it is important to maintain safety gear and the practical maintenance tips.
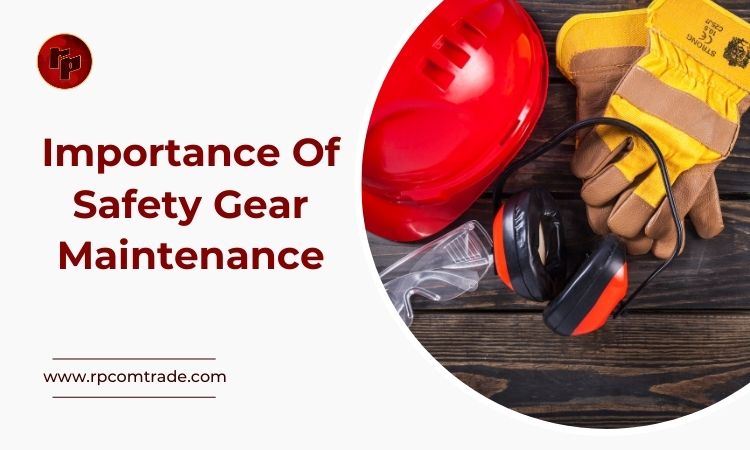
Why Is Safety Gear Maintenance Important?
Regular maintenance of safety gear ensures that the equipment functions correctly and effectively protects users from harm. Routine inspections and repairs address wear and tear, adjust fit and clean the gear, which prevents equipment failure and reduces the risk of accidents. Proper upkeep extends the gear’s lifespan and maintains its adherence to safety standards, fostering confidence in its reliability and contributing to a safer environment.
Here’s a detailed breakdown of how well-maintained safety gear impacts various aspects of workplace safety:
Durability
Regular maintenance extends the life of safety gear by addressing wear and tear before it causes serious issues. This proactive approach prevents sudden failures and ensures the equipment remains reliable and effective over time.
Protection
Maintenance ensures that safety gear continues to offer the intended protection. Well-maintained equipment performs its protective role effectively and meets safety standards, safeguarding workers from specific hazards.
Cost Savings
Routine upkeep reduces costs by extending the lifespan of safety gear, avoiding premature replacements, and preventing costly repairs. It also minimizes downtime, which saves money on lost productivity.
Employee Confidence
When safety gear is well-maintained, employees feel more secure and confident in their equipment. This boosts morale, enhances job satisfaction, and encourages adherence to safety protocols, contributing to a safer work environment.
Building a Positive Safety Culture
Building a positive safety culture within an organization offers numerous advantages that contribute to a safer and more productive work environment.
Commitment to Worker Safety
A strong safety culture shows a genuine commitment to worker safety, leading to better protective measures and fewer accidents. Employees are more engaged in safety programs, and the organization remains compliant with safety regulations, reducing legal and financial risks.
Safety Mindset in the Workplace
Promoting a safety mindset encourages employees to stay aware of hazards and follow safety protocols. This proactive approach helps prevent accidents, fosters continuous improvement, and creates a supportive work environment that boosts morale and productivity.
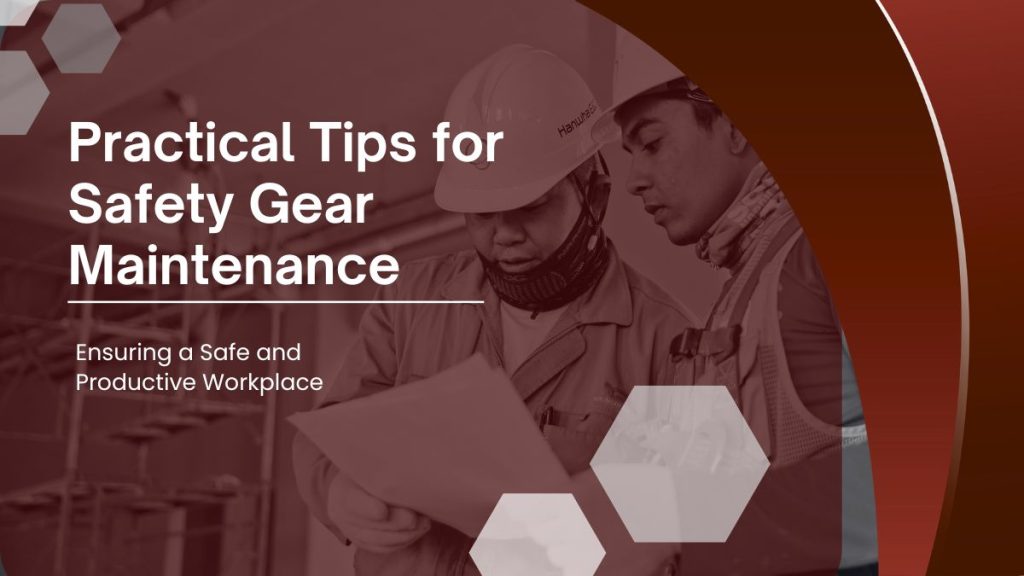
Practical Tips for Safety Gear Maintenance
Effective maintenance of safety gear is essential for ensuring its reliability and performance, which directly impacts workplace safety. Here’s a detailed breakdown of practical tips for safety gear maintenance:
Routine Inspections Based on Gear Type and Usage
Regularly inspect safety gear based on its type and usage. Check helmets for cracks and worn padding, gloves for tears, eyewear for scratches or cracks, and respirators for filter expiration and proper fit. These inspections help identify issues early, preventing equipment failure and ensuring safety.
Employee Training on Proper Cleaning and Storage
Train employees on the correct cleaning methods and storage practices for safety gear. Use appropriate cleaning agents and store gear in a clean, dry place away from extreme conditions. Proper training helps extend gear life and ensures readiness for use.
Record-keeping of Inspections, Repairs, and Cleaning
Keep detailed records of inspections, repairs, and cleaning activities. Log dates, conditions, and issues to track gear history and schedule maintenance. Accurate record-keeping supports proactive management and maintains gear effectiveness.
Follow Guidelines
Adhere to manufacturer instructions and industry standards for cleaning, maintenance, and storage. Following these guidelines ensures gear effectiveness, compliance with safety standards, and reliable protection for employees.
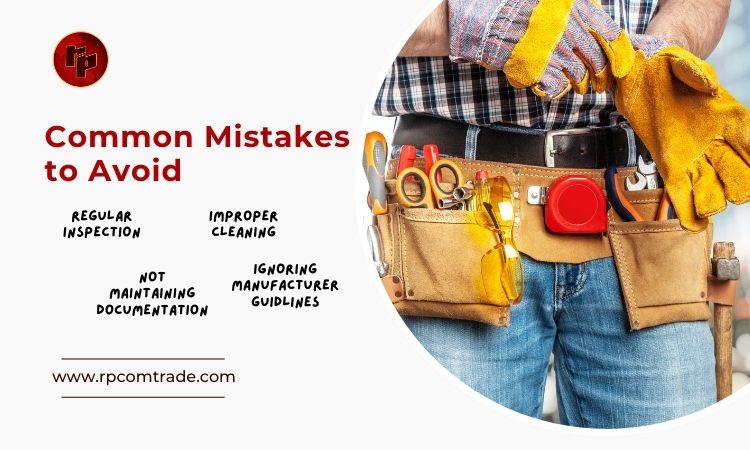
Common Mistakes in Safety Gear Maintenance
Effective maintenance of safety gear is essential for ensuring that it provides reliable protection and performs as intended. However, several common mistakes can undermine maintenance efforts and compromise workplace safety.
Here is the list of common mistakes:
Neglecting Regular Inspections
Failing to conduct regular inspections is a common mistake in safety gear maintenance. Without routine checks, issues like cracks, wear, or damage can go unnoticed. This oversight increases the risk of equipment failure, which can lead to unsafe conditions and higher chances of accidents or injuries, as compromised gear may not offer adequate protection when needed.
Improper Cleaning or Storage
Improper cleaning and storage can significantly impact the performance and lifespan of safety gear. Using incorrect cleaning agents or neglecting regular cleaning can damage the gear’s materials, reducing its effectiveness. Additionally, storing gear in environments with extreme temperatures, moisture, or direct sunlight can lead to deterioration of its components. Adhering to proper cleaning and storage practices is crucial for maintaining the gear’s integrity and ensuring it remains safe to use.
Ignoring Manufacturer Guidelines
Ignoring manufacturer guidelines for maintenance, cleaning, and storage is a critical error. Manufacturers provide specific instructions designed to ensure that safety gear remains functional and effective. Deviating from these guidelines can result in improper maintenance, potentially rendering the gear unsafe or ineffective. Following the manufacturer’s recommendations is essential for preserving gear performance and meeting safety standards.
Not Maintaining Documentation
Failing to keep proper documentation of inspections, repairs, and cleaning activities can create gaps in safety management. Without accurate records, tracking the gear’s condition, scheduling necessary maintenance, or identifying recurring issues becomes challenging. Maintaining detailed documentation supports effective management by providing a clear history of gear upkeep and ensuring that all maintenance tasks are completed as required.
The Bottom Line
Maintaining safety gear is crucial for ensuring its effectiveness and protecting employees from hazards. Conducting regular inspections, cleaning gear properly, storing it correctly, following manufacturer guidelines, and keeping detailed records are essential practices that keep safety gear in top condition and prevent equipment failure. Addressing common maintenance mistakes and implementing these practices helps organizations reduce the risk of accidents and create a safer work environment. To ensure ongoing safety and optimal gear performance, adopt regular inspection routines and uphold stringent safety protocols, fostering a proactive safety culture within the organization.